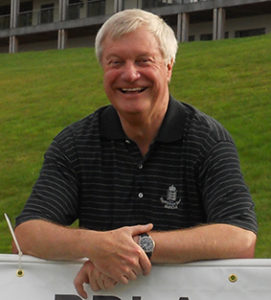
In un momento in cui la pandemia globale sta mettendo in crisi la salute pubblica e cambiando radicalmente il comportamento dei consumatori nel commercio al dettaglio, Nick Coombes (NC) intervista in esclusiva Paolo Grasso (PG), Head of Sales per la Label Business Unit di OMET Srl, sui trend attuali del settore e su come sta rispondendo OMET alle nuove condizioni di mercato.
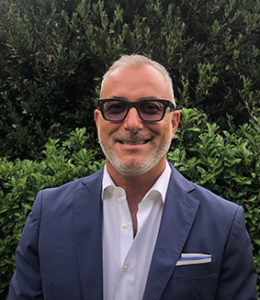
NC: Il confronto fra flexo in linea o a tamburo centrale (CI) non è un argomento nuovo: come vede il settore flexo in questo momento?
PG: “L’industria ha passato anni a discutere quale sia la strada migliore da percorrere e, sebbene non ci sia una risposta semplice, le considerazioni non sono cambiate molto: dipende dagli obiettivi e dalla tecnologia preferita. Entrambe usano la tecnica di stampa flessografica, ma è proprio qui che finiscono le somiglianze”.
NC: Riguarda più l’applicazione che la tecnica?
PG: “Sì, perché i due diversi modi di utilizzare il processo flessografico determinano in gran parte il prodotto finale. Quindi, prima di approfondire l’argomento dobbiamo stabilire chi fa che cosa e perché. Dobbiamo guardare dietro le quinte e vedere come i due processi si sono sviluppati fino a oggi”.
NC: Come vede la situazione attuale della tecnologia CI?
PG: “La sua crescita negli ultimi anni è stata in parte stimolata dal calo delle tirature dei prodotti che tradizionalmente venivano stampati su rotocalco, tecnologia meno adatta a lavori con piccole tirature. Dal punto di vista della qualità, la flessografia CI a base solvente può sostituire in modo sufficiente la rotocalco a base di solvente, ma i costi di investimento e di esercizio sono significativamente inferiori se si considerano prestampa, stoccaggio, configurazione e così via. Una macchina da stampa flessografica CI ha anche un ingombro ridotto ed è più facile da usare e mantenere. Le tecnologie concorrenti servono principalmente lo stesso mercato, vale a dire gli imballaggi flessibili primari per il settore alimentare e delle bevande, e continuano a farlo in volumi elevati su larghezze del nastro tipicamente di 1,3 m o più. Ma la tendenza è quella di tirature più brevi su macchine da stampa più strette, con i produttori che riducono le dimensioni fino a 850 mm o addirittura fino a 670 mm di larghezza nastro”.
NC: Qualche confronto con il processo flessografico in linea?
PG: “Essenzialmente il processo in linea si è sviluppato partendo dalla tecnologia del nastro stretto che ha avuto inizio nel primo dopoguerra come mezzo per produrre etichette. Negli ultimi decenni questo settore ha registrato un alto tasso di crescita poiché è aumentata la domanda di porzioni più piccole in confezione singola e una maggiore differenziazione dei prodotti. Si tratta di un mercato molto abituato all’uso di inchiostri e lacche UV, con l’ultima tendenza verso la polimerizzazione LED / UV per motivi di maggiore efficienza e minori costi di esercizio”.
NC: Da dove viene questa crescita nel narrow web?
PG: “Il mercato delle etichette autoadesive è cresciuto in termini di volumi, materiali ed applicazioni. Ad esempio, l’industria della birra, che un tempo era dominata dalle etichette stampate in offset a foglio e applicate con colla, è recentemente passata al film autoadesivo che migliora l’aspetto e quindi la qualità percepita del prodotto. Consente inoltre un ciclo di vita più lungo del marchio sulla bottiglia. Altre aree di crescita significativa riguardano i film per shrink sleeves e le etichette IML che tipicamente utilizzano supporti in PVC, PETG e BOPP. Immaginando la dimensione di una sleeve termoretraibile con le sue decorazioni a 360 gradi, e confrontandola con un’etichetta tradizionale, è chiaro perché la domanda di macchine da stampa in linea con larghezze di nastro più ampie sia cresciuta nel tempo. In questo settore di mercato, i 430 mm (17″) sono normali, ma i 530 mm (21″) e i 670 mm (26″) stanno entrambi diventando sempre più popolari”.
NC: Il mercato ha colto velocemente questa tendenza?
PG: “Sì, soprattutto in Asia. Le sleeve hanno una superficie più ampia che consente una migliore veste grafica, più accattivante e offre più spazio per le informazioni. Ha effettivamente cambiato interi settori del mercato e ha offerto ai brand l’opportunità di differenziare i propri prodotti da quelli dei concorrenti. E’ interessante che in Asia la rotocalco sia ancora il processo di stampa preferito per le shrink sleeves, ma nel resto del mondo la flessografia in linea con UV, narrow web, è riconosciuta da tutti come la più adatta”.
NC: Stiamo raggiungendo un punto di incontro tra CI e inline?
PG: “Abbiamo una situazione in cui i volumi complessivi stanno aumentando, ma lo è anche il numero di SKU (Stock Keeping Units, quantità di merce a magazzino), il che significa effettivamente tirature più brevi per una maggiore varietà di lavori. Nel caso delle shrink sleeves e delle in-mould labels, possono essere stampate con entrambe le tecnologie, motivo per cui si vede crescere la fascia delle macchine in linea e diminuire su quelle a tamburo centrale. Direi che il punto d’incontro è sui 670 mm – 850 mm (26″- 33″) – lo si può dire dal numero di produttori che hanno sviluppato una nuova tecnologia in quel formato. È la fascia in cui i cambi rapidi facilitano la gestione di tirature più brevi a un costo commercialmente più sostenibile”.
NC: Quindi, un converter potrebbe scegliere indifferentemente uno dei due processi per competere sul mercato?
PG: “Non esattamente, perché dipende dal tipo di lavoro che sta cercando di produrre e dai settori di mercato che fornisce. L’approccio in linea si basa principalmente su tecnologia LED/UV, mentre il mondo CI è ancora prevalentemente dominato dal solvente, e questo si riflette sulla qualità di stampa dei packaging. Il LED/UV è molto più vicino alla stampa rotocalco in termini di qualità, mentre la stampa a base solvente è più economica. Se si guarda all’industria alimentare, per esempio, attualmente non c’è quasi interesse verso il LED/UV per l’imballaggio primario, ed è qui che i converter in linea stanno combattendo le loro battaglie più dure. Sono stati compiuti progressi con inchiostri e lacche a bassa migrazione, ma siamo ancora lontani da un processo industriale. È qui che la tecnologia CI è forte e, in tutta onestà, è probabile che rimanga la tecnologia di riferimento per il prossimo futuro. L’unico cambiamento potrebbe essere la maggiore diffusione della asciugatura Electron Beam, ma solo se i livelli d’investimento e di esercizio diminuiranno in modo significativo”.
NC: Ci sono altre considerazioni quando si decide se scegliere inline o CI?
PG: “A parte le considerazioni sulla qualità menzionate in precedenza, il problema principale sono i volumi. La maggior parte delle moderne macchine da stampa CI girano a 450 m/min o più, su fasce anche superiori a 1,3m, quindi sono impostate per volumi elevati. Il processo in linea proviene dal mondo delle etichette autoadesive, dove 200 m/min è una velocità alta su fasce solitamente attorno ai 430mm. C’è una grande differenza di fondo: i converter che utilizzano tecnologie CI misurano la produzione in tonnellate, mentre quelli che utilizzano macchine in linea sono abituati a ragionare per pezzi (poi convertiti in metri lineari). Una tiratura breve su una rotativa CI potrebbe essere di 1 tonnellata, mentre su una macchina in linea parliamo di 300kg ed a volte anche meno. Non c’è modo di pensare di produrre tirature così brevi su macchine a tamburo centrale”.
NC: Ha esempi di converter che utilizzano un mix di queste tecnologie?
PG: “Sì, abbiamo un caso molto interessante nel mercato italiano. Una grande azienda di stampa che ha da poco acquisito una realtà più piccola ma molto efficace, con quattro linee flessografiche OMET a LED specializzate su lavori di brevissime tirature. Per il 90% riguardavano l’imballaggio primario di alimenti diretti, dove l’assenza di odori e contaminati è fondamentale. La casa madre invece opera esclusivamente con macchine da stampa rotocalco e flexo CI a solvente che riforniscono gli stessi brand owners. L’unica differenza sta nelle tirature: le linee OMET sono economiche fino a 1.200 metri lineari, eseguono tipicamente basse tirature, anche da 300kg di film laminato, con minimi da 100kg per ordini speciali. Non è pensabile produrli in modo così economico su una rotativa CI”.
NC: In sintesi, quali sono i fattori chiave nella scelta tra le due tecnologie?
PG: “La qualità ed il time to market sono secondo me i fattori decisivi. Che qualità deve avere e quanto velocemente puoi consegnare? Questi sono i problemi che oggi tutti affrontano nella stampa di imballaggi. I brand owners vogliono il meglio, lo vogliono economico e il prima possibile: non è un problema facile da risolvere per i converter. Ma ciò che sta diventando sempre più evidente è la necessità di una produzione flessibile e di un modello di business sufficientemente agile per reagire rapidamente ai cambiamenti della domanda dal mercato. Questo è un argomento molto valido per propendere verso le tecnologie in-line. Tirature più brevi, più SKU, consegne più veloci e maggior valore aggiunto: sono tutti fattori che il settore del narrow web ha risolto con successo negli ultimi anni, quindi il know-how e la tecnologia sono ben consolidati. Dove la tecnologia CI ancora tiene è sui volumi alti e sugli imballaggi alimentari primari in cui la migliore qualità di stampa non è il drive principale. Ognuno ha il suo ruolo sul mercato”.
NC: Passando dalla CI alla flessografia in linea, vede la stampa digitale influenzare questo settore di mercato?
PG: “La domanda di stampa digitale sta crescendo rapidamente e ci sono molti esempi ben consolidati nel mercato globale, ma il costo è ancora un fattore prevalente, e fino a quando non cambierà vedo il digitale come una tecnologia complementare piuttosto che sostitutiva. Nessuna singola tecnologia può essere considerata la migliore in ogni campo. OMET ha approcci diversi proprio per poter offrire la più ampia gamma di soluzioni ai propri clienti”.
NC: Può spiegare meglio questo punto?
PG: “Prima di tutto offriamo macchine flessografiche UV/LED nel settore del narrow web, come ho già detto. Ma il design della nostra piattaforma consente di fornire una varietà di soluzioni di stampa ibride in diverse configurazioni. Ad esempio, abbiamo fornito ai clienti macchine da stampa ibride che combinano unità di stampa offset/flexo/rotocalco, tutte in fascia stretta, in linea, e che utilizzano una combinazione di sistemi di asciugature a solvente, UV od EB. Questa combinazione di tecnologie consente ai converter di ottenere una qualità imbattibile al minor costo possibile. Ad esempio, i costi di prestampa offset sono trascurabili, il che consente ai trasformatori di buttare letteralmente via le lastre di un lavoro che non venisse ristampato perché il prodotto non ha avuto (ad esempio) successo nella fase di lancio. Inoltre la qualità e la risoluzione della offset non possono essere eguagliate dalla flessografia e possono essere confrontate solo con la rotocalco”.
NC: Cosa offre una linea ibrida ai converter?
PG: “Faccio un esempio: per ridurre al minimo il costo della posa di un bianco a fondo pieno mantenendo le densità adeguate, integriamo una stazione rotocalco nella linea di stampa. L’inchiostro bianco a solvente è molto economico e la copertura è la migliore che ci si possa attendere. Alla fine il cambio lavoro si riduce ad un solo gruppo stampa sull’intera macchina. Per una completa compatibilità alimentare stampiamo offset wet-on-wet e quindi utilizziamo un sistema di asciugatura EB per polimerizzare tutti i colori e le vernici in un unico passaggio. L’asciugatura EB non richiede fotoiniziatori, quindi non esiste alcun rischio di migrazione e contaminazione”.
NC: Quali altre soluzioni ibride sono commercialmente interessanti?
PG: “Prima ha accennato al digitale: un concetto molto simile di processi di stampa ibridi è la combinazione flessografia/digitale che ottimizza i costi senza sacrificare la qualità. Dal 2017 collaboriamo su base di reciproca esclusività con Durst per integrare i loro motori di stampa RSC in una macchina che abbiamo chiamato OMET XJet. Questa macchina da stampa è destinata al mercato delle etichette adesive ed alle shrink sleeves, grazie alla tecnologia inkjet da 1200×1200 dpi con gocce da 2pl, all’efficienza dei costi delle lastre flessografiche, ed al converting in linea”.
NC: Qual è l’applicazione tipica di questa tecnologia ibrida?
PG: “Se un converter ha bisogno di fare una tiratura di prova per la campagna di marketing di un suo cliente, può stampare il lavoro interamente e molto economicamente in digitale, con un clichè flexo per il bianco di base. Questo offre grandi risparmi sul costo di stampa di un bianco digitale, pur consentendo una tiratura di 100 immagini tutte diverse tra loro! Devi decidere che cosa devi fare prima di determinare la configurazione di qualsiasi macchina da stampa ibrida, e poiché i brand owner ed i converter cercano maggiore differenziazione, saranno quelli con maggior immaginazione a trarne maggiori benefici”.
NC: Come vede il mercato negli anni a venire?
PG: “Non sono un indovino, ma la mia sensazione è che il digitale prenderà sicuramente sempre più quote di mercato. Ciò non significa che le tecnologie di stampa tradizionali scompariranno. Al contrario, coesisteranno e si completeranno. “Ibrido” diventerà un termine comune nel nostro settore ed in pratica ciò che OMET sta facendo oggi diventerà uno standard diffuso nel medio termine: poter scegliere da un cesto di tecnologie miste per creare nuove e illimitate configurazioni che si adattano perfettamente alle esigenze dei clienti di domani”.