Just over two years have passed since the first interview with Edoardo Fonti, a young and dynamic entrepreneur who, since 2017, has approached the flexo printing and converting market with the company Eco Air. Today, thanks to the desire to grow and invest in the sector, the offer has extended to wastewater washing, treatment and regeneration plants, thanks to the newly established ECO FLEXO srl
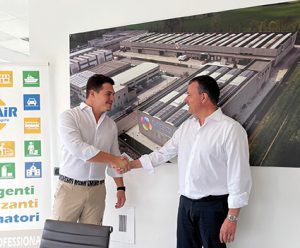
Returning from the positive participation in Print4All, where for the second time Eco Air presented its line of professional detergents for inks and glues, ECO FLEXO made its debut by presenting itself at the fair with a complete package of cutting-edge systems, also presenting the new 2022 catalog. We meet Edoardo Fonti, owner of the company, at Mulazzano (Mi) office, together with Massimo Gionta, who as a direct agent of Eco Air is now involved as a partner at new ECO FLEXO.
Since January 2020, when this collaboration began, the name of Eco Air has begun to circulate more and more also in printing and converting companies, thanks to an offer of specific cleaning products for the sector, a strategy that is it proved to be a winning one and which encouraged the company to create a division for the design, construction and assembly of systems specific to the needs of flexo, even managing in a very short time to develop systems with international patents.
From cleaning products to dedicated technologies
Today, thinking of being able to be attractive with only an offer of specific products for cleaning and detergent inks and glues, without thinking of not having to deal with the battle of low prices is almost a chimera. Hence, in January 2022, ECO FLEXO was born with Edoardo Fonti as owner, flanked by Massimo Gionta as partner, as well as sales manager for Italy.
“We decided to offer our customers a complete package ranging from the detergent to the cleaning system up to the treatment of wastewater derived from washing and various productions”, says Edoardo Fonti.
The new company therefore deals with the design, construction and marketing of cleaning systems, distillers and waste water treatment, with specific solutions for the world of flexible packaging, labels but also corrugated cardboard, so as to offer the customer a complete package of products and systems.
“There are companies on the market that sell detergent products, others that offer systems, but there is no reality that can offer consumable and technologies. With ECO FLEXO we are going to fill a market gap and we are sure that this is the right way to grow further, offering our customers a single point of contact for their cleaning needs”, Massimo Gionta intervenes. By virtue of the great specialization required, ECO FLEXO has selected for Italy some agents, well known on the market, each of which will deal only with one sector, however covering the entire offer for printing, from flexible to labels, from corrugated cardboard to tissue, a model that will then be replicated abroad as well.
The new induction solvent distiller with international patent
A specialized engineer was also involved in the new company, with a deep know-how in the design of plants of this type, exploiting the synergy with the three Eco Air chemists to develop together plants with increasingly higher performance and capable of enhancing the combination of plant for detergent/plant for wastewater.
One of the first projects that have been developed by the new team is the new distiller, covered by an international patent, which no longer works with diathermic oil but with induction, eliminating the consumable product, in this case diathermic oil, that is difficult to find in the last period, eliminating the waste of energy for the start-up times to heat the oil and at the end of the cycle to cool it, reducing maintenance interventions.
“All distillers for solvents to date have used a technology that provides for the heating of diathermic oil inserted in a cavity of a boiler by means of resistors. Once the temperature is reached, the diathermic oil transmits the heat to the solvent present in the boiler, making it evaporate and thus separating the dirty and polluting solvent. The solution patented by us is instead an induction technology: the heat, thanks to an electromagnetic resistance that creates it, is transferred directly inside the boiler where the dirty solvent to be treated is deposited. By eliminating diathermic oil, one of the first advantages is certainly satisfying the demands of increasingly ecological processes, eliminating the purchase and disposal of used oil. Another advantage concerns the waiting time for the extraction of the clean solvent, practically immediate once the distillation cycle is finished, unlike oil which instead required the heating time at start-up and cooling at the end of the process, which can last even 2 hours”, says eng. Roberto Giglioli, project manager, also stressing that with this new technology there is also a great energy saving, in fact the energy required is reduced by up to 20% per distillation cycle.
“This new distiller is a source of great pride for us, we have launched a worldwide novelty, and today we can say that we are the only ones on the market with this type of technology”, says Edoardo Fonti, specifying that in any case the offer by Eco Flexo also includes standard diathermic oil distillers with sizes ranging from 12 liters manual up to 1200 liters automatic.
Solutions for the world of flexible packaging and labels
A horizontal cliché washer was developed for washing needs of flexible packaging and label plates, available in various sizes and various configurations, to meet all the various operating and budget requirements.
Fully automatic washing, rinsing and drying function, and self-regulation based on the thickness of the cliché to be washed. This system is also protected by an international patent, by virtue of the standard cliché feeder and conveyor belt, which avoids the manual intervention of the operator, ensures a more accurate procedure and reduces system maintenance.
Various options are also available, such as heating the detergent, the configuration for the use of the solvent according to ATEX certification.
For the label sector, the ultrasonic anilox washer was presented during Print4All, a compact bench-top system that allows you to simultaneously wash two anilox/sleeves with a length of 500 or 1000 mm.
Another system developed for the label industry is the pieces-washer, with and without solvent, which allows in a single cycle, the washing of the whole set, consisting of cylinder, tray, doctor blade, with the possibility of choosing the washing/blowing version or washing/rinsing/blowing.
Specific solutions for the paper converting and corrugated cardboard sector
For printing cliché washing needs of the paper industry and corrugated cardboard, a vertical cliché washer has been developed with central opening for easy positioning of the cliché, with fully automatic washing, rinsing and blowing cycles. Thanks to the double diaphragm pump for the recovery of the product from the tank and re-injecting it to the tanks, the deposit of liquids inside the tank is avoided once the washing cycle is finished, to reduce maintenance and cleaning operations of the system, which is also ready for industry 4.0.
Another solution dedicated to the world of paper converting is the system for washing buckets, drums or tanks for cleaning them with timed pneumatic washing cycles, with an average cleaning time of 3 minutes. An integrated, heated container ensures efficient fluid handling.
The system is extremely compact, does not require any installation, and being easily transportable, it can be moved where the company needs it. “This is one of those small systems that any printer who has an internal color kitchen or InkMaker should have. Avoid wasting time, manual cleaning of the buckets, which never takes place in a thorough and accurate manner, and also thanks to the excellent cost/benefit ratio, allows an immediate return on investment”, adds Edoardo Fonti.
Finally, always dedicated to the world of cardboard, we find purifiers and clarifiers for printing wastewater so as to be able to reinsert them, once the treatment has been carried out, in the production or washing cycle, or through activated carbon filters, dispose of them directly into the sewer system. For this type of systems it is possible to request customization based on the needs of the company.
“Our plants are able to purify the waste water from ink residues, glues, starches and various scraps; it is a plant with excellent performance, with low energy consumption and high hourly productivity. We need to think more and more about the future, not only of our companies but also of the planet”, companies increasingly have a green vision, and the recovery of wastewater is not only an economic saving, but it is a simple way to avoid increasing pollution”, adds Edoardo Fonti.
A catalog for all needs
The range includes a series of products that can support printers and converters of any sector, high-pressure ultrasonic anilox washers, or the laser system, which is the only technology not developed internally but which has been included in the catalog for completeness of range, horizontal and vertical cliché washes, dry washing systems, distillers for solvents and waste water treatment systems, manual washes for screen printing frames, etc.
The whole range of chemical products for the detergency and cleaning of inks and glues both in manual version and logically for the various automatic systems, where the famous SHARK ECO stands out for the manual cleaning of aniloxes”, a product that we believe is indispensable for every printer and who is giving us great satisfaction”, Gionta intervenes.
“Obviously engineering inhouse internal products and technologies, we offer an after-sales service with qualified internal staff both in Italy and abroad, a topic that should not be underestimated”, concludes Edoardo Fonti.