The reliability and speed of these machines have convinced this giant of paper food bags industry to acquire 7 Matador NG, from the German company Garant, part of Windmoller & Holscher group
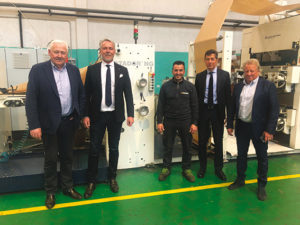
Turconi has its operational headquarters in Ceriano Laghetto (MB) and has been operating in the production and direct distribution of food bags for over 65 years, because it was 1953 when Agostino Turconi founded a small company in Saronno, devoted to the marketing of paper products.
In 1962 the reins of the company passed into Renato Turconi’s hands, Agostino’s son; 1970 is the turning-point year when the first machineries were bought and began the internal production of printed paper. Since then the company has been walking beside big brands, since they had only small outlets, starting with them a path of constant growth.
In the 80s new machineries were introduced according to a process of constant renewal and evolution which has been followed by Turconi from the very beginning. The group extended, new highly technological plants are patented for the production of paper bags.
The numbers of Turconi, that now has 8 collaborators, are impressive: 4.000.000 million paper bags and 200 quintals of poly-lined and laminated paper manufactured every day, 15.000 sm covered area in central in the headquarters, 150 kinds of sold products, 26 production lines and 5 warehouses displaced in the Italian territory (Ferrandina – MT, Falconara Marittima – AN, Roma, Termini Imerese – PA; Cagliari).
Turconi’s position in relation to the environment is very clear. The company is endowed with a photovoltaic system that develops an output of 600 kWp, able to satisfy the energy needs of all machineries. The company, in order to emphasize its commitment and attention to environmental issues, created the line I Love Nature, that combines ease of use with a young and eco-friendly style.
Target-oriented investments and exclusive technologies
At the moment, the company has the highest numbers of production lines all over Italy and is the only one that can rely on an automatic and continuous production cycle, from web placing to packing in shrink-wrapping material. Thanks to this plant, paper bags are never handled by the staff and they are stored in packages containing a number of guaranteed pieces, according to customer’s requirements.
During its development Turconi has reached a production department consisting of 22 latest-generation bag machines, equipped with fully automated systems and 3 food paper production lines.
In 2013 Turconi Industria, a company formed by Turconi and Bonucci, with a new seat in Gerenzano (VA), started its production to satisfy central and southern Italy with further 11 bag machines and three printing machines and food paper laminating. Quality, innovation, development and professionalism are the qualities that have enabled the two companies to consolidate their position as an optimal and qualified partner for the GDO. An excellent technical/production team, led by Silvano Scarano, has allowed the Turconi group to create an optimal management of all machines.
The new bag machines by Garant – W&H
The machines that Turconi and Turconi Industria installed over three years are seven: four Matador NTG and three Matador SIM.
The MATADOR NG is the right machine for a fast and efficient production of flat and satchel bags with perforated top edge and with side gussets, high reliability and speed of this equipment convinced us; the machine is equipped with innovative characteristics like perforation with direct drive technology, recipes management, patented bottom pasting system and high automation, that together guarantee more efficiency and make possible a low cost and competitive bag production”, says Turconi.
Besides the machine can be equipped with the following options: device for window, window patching machine SERVO, valve group, electric-pneumatic punching machine, Linaflex NL (inline printing unit), wicket hole punching SERVO with strengthening slip of paper and micro-perforation.
The other machines ordered are the Matasim, a model presented in 2018 in Chicago at Pack Expo, that completes the range of Matador bag machines. When it was developed, the aim of Garant was above all the ease of use. “We needed an equipment able to produce paper bags quickly and minimum effort for operator, and also the fact that the machine requires low maintenance was another important quality for us”, explains Turconi. To obtain this result the accessibility to the individual machine components has also been optimized, making the machine especially user-friendly. The design of the machine is robust and commissioning is very quick.
“This product embodies German engineering and addresses users looking to produce simple products on a correspondingly low-priced machine, and, as for all Garant machines, is proposed a suitable printing unit, LinafleX S. The MATASIM is a particularly compact machine that can be incorporated into any production environment.