Four years later, we return to visit Termoplast Nord, faithful for almost twenty years to printing technology of Koenig & Bauer Flexotecnica, a trust confirmed by Dante Zecchel, sole director of Termoplast Nord, also for this last new particular project
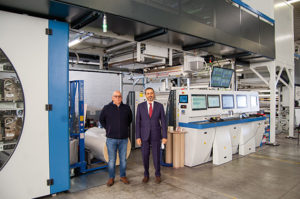
Defining this company in the province of Treviso specialized in the production of flexible packaging does not reflect correctly the corporate philosophy that has always focused on the production of packaging with an attentive care to environmental impact, thanks to cutting-edge technologies and environmentally sustainable materials.
16 product sectors served, from clothing to food, passing through bags for transporting documents, up to the sector of silicone-coated PE and PP films for soil and pellets. One plant in Giavero del Montello (Tv), and production plants in India, Asia, North Africa, because being present in fast growing markets is important for a company that aims to grow also at international level.
A production workflow that starts from raw material (9 extruders, one of which is dedicated to the production of bio film), to printing with 7 flexographic machines, laminating and final converting of reels, is the strength of an entrepreneurial idea that has not chosen only one sector, but takes advantage of the transversality of its technologies, which combined with an R&D department in which about 5% of turnover is invested, allow Dante Zecchel, an entrepreneur in the true sense of the word, to seize all the opportunities that the market presents to him.
Innovative and modular technology to win new challenges
“From Covid-19 emergency a series of projects have started that see us personally involved, together with Politecnico di Milano and other companies, for the production of special antibacterial films to make covers for books and notebooks, a new sector on which we are focusing a lot in the near future”, Dante Zecchel begins. There is certainly no shortage of production technologies in Termoplast Nord, investments are constant but listening to its founder one gets the feeling that the classic 48-hour day would be needed. It becomes therefore essential not to be overwhelmed by the emotionality of the moment and keeping that cool head that every entrepreneur should have in the salient moments of his history, trying to sniff out new trends and opportunities.
This premise is a must also in reference to the latest investment that saw Termoplast Nord confirm its trust in Koenig & Bauer Flexotecnica.
The installation of a new latest generation 8-color EVO XD flexographic printing machine dates back to the end of 2019, with all automation and controls for checking the print quality and also equipped with a gravure printing unit in the delivery part, the real peculiarity of this installation. The choice of adding a gravure unit is not usual in the wide web world as opposed to what happens now in standard configurations in label printing machines. “This installation represents a bet for us, we have some ideas on the markets to go and conquer, but we know we have a great challenge ahead of us. I am sure that thanks to this investment we will be able to further expand our customer portfolio, since until now we were not equipped for this type of request”, says Zecchel.
Flexo printing with in-line gravure unit for cold seal application
A machine with such a configuration will be able to exploit the gravure unit for the application of cold-seal on the film for the production of heat-sealing food packaging, in a single step. For example, think of packaging of wafer biscuits, which traditionally use these types of packaging printed on polyester or polypropylene, laminated with aluminum or metallized films and inside the cold sealing that can only be achieved by means of a gravure unit. Obviously, all the finishes on the film, with coatings, soft-touch effects and so on, are also easier to achieve using the gravure unit. “We have a very active Research & Development department and we work in close collaboration with our customers to develop highly performing and innovative products capable of truly responding to the sustainability needs we should all aim for. We have recently developed a biodegradable, compostable film with the addition of antibacterial agents capable of meeting the new safety needs required by the market”, adds Zecchel.
“Choosing, as in the case of Termoplast Nord, the gravure unit means wanting to broaden horizons towards new opportunities, since through a versatile element it is possible to offer the customer new applications for their packaging needs. The EVO XD present here in Termoplast Nord was conceived from the beginning with the gravure unit in line, even if, actually for the customer’s needs, the system was installed at the end of 2019 while the addition of gravure unit, initially planned for March of this year was then effectively completed in October due to Covid emergency.
The EVO XD model has been designed to be easily upgradeable with additional units online, even at a later time, just as happened on this occasion. It was enough to move the winding unit to allow the insertion of the gravure element and complete the installation”, says Andrea Dallavalle, Sales Director Europe of Koenig & Bauer Flexotecnica, underlining that the gravure module was designed and built entirely in-house in Koenig & Bauer Flexotecnica plant of Tavazzano (Lo), also thanks to the know-how deriving from having been part of Cerutti Group for many years.
Winning partnerships for a very high quality flexo
“Even in flexible packaging the idea of adding value to printing is gaining ground and doing it where possible in line with the printing machine, therefore we will see more and more configurations with elements in line, whether they are flexo, gravure, lamination, coating. This type of configuration can also be ideal for those brand-owners who are used to printing their packages in gravure, and who, reassured by the presence of additional units in line, indispensable as we have seen for the application of cold-seal, they could decide to take the plunge and test the quality of flexo”, concludes Dallavalle.
Precisely with regard to the opportunities for the flexographic world to approach jobs and customers traditionally linked to the gravure world, Termoplast Nord together with Fotolito Veneta and Simec has created a working group for the study of a new stochastic screen and a new anilox, to achieve gravure printing quality. “In this way we are able to raise the color density using purer pigments, without the need to dilute them, obtaining cleaning of screen and optimal minimum dots, so it is possible to print shades practically close to zero. We have become suppliers of very important brands, deeply linked to the quality of gravure printing, but when we put them in front of our results, we were able to convince them that switching to flexo would be the right choice for them”, concludes Zecchel.