Leipzig University of Applied Sciences (HTWK), Institute for Printing, Processing and Packaging Leipzig
by Kilian Menzel, Natalie Früholz, Lucia Görbert, Lutz Engisch
Gravure printing offers great potential for the circular economy, its major ecological advantages are the re-usability of the printing cylinder and closed material cyles which enhances the sustainabilty of the gravure process. Generally the ecological impact of the various printing processes depends on many different factors and require a case-by-case consideration for every application and print job. Current innovations of the gravure process aim to further improve its sustainability.
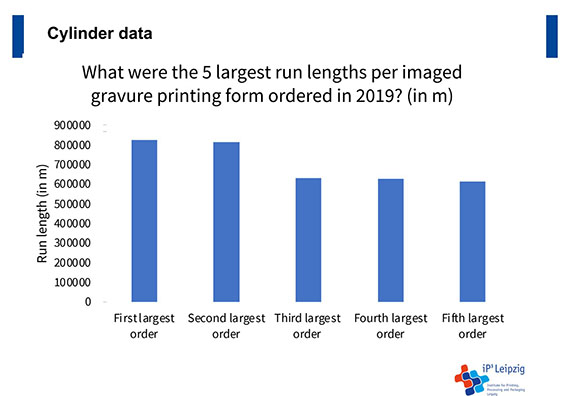
These are the conclusions of a survey on the sustainability of the gravure process carried out by the Leipzig University of Applied Sciences. The study, which is based on a questionaire and interviews within the gravure industry, was conducted in the first half of 2022 and recently presented by Prof. Lutz Engisch (Leipzig University) at ERA´s Annual & Packaging/Decorative Conference in Baveno, Italy. In the study, that was initiated by ERA, it is also referred to current innovations to further improve the sustainability of gravure such as the recovering of solvents and alternatives for chromium trioxide in cylinder plating.
The online questionnaire was conducted from 14. Feb 2022 to 1. Jun 2022 and addressed more than 116 contact persons. It included questions to all stages of the rotogravure printing workflow and includes upstream and downstream processes, e.g., cylinder engraving and transportation as well as recycling and deinking. Based on the defined role in the gravure printing industry, the survey contained a certain selection of questions, which are specifically addressed to these stakeholders. Survey respondents are very concerned with sustainability, with 43 % indicating very familiar and 48 % indicating moderately familiar with the issue of ecological sustainability within the gravure printing industry.
The reusability of the base cylinder is perceived as the strongest advantage of gravure printing. Further strong improvements concerning the sustainability of the process were seen in the use of and the reduction of emissions of hazardous chemicals. Within the respondents, the electrolysis process of chromium trioxide (CrVI) is perceived as the strongest challenge for gravure printing.
Approaches for further improving the sustainability in the future were seen in recovering solvent, using lower ink film to save ink, the substitution of CrVI and reducing make-ready waste (e.g., through automation).
Above all, the interviews revealed a desire for better communication and coordination throughout the entire supply chain. This includes all players from ink manufacturers, machine builders, design agencies to recycling companies. This exchange could facilitate the coordination and prioritization of developments to sustainably improve environmental factors.