With 2 production plants in Inzago (Milan) and Marano Vicentino (Vicenza), 3 commercial offices in England, Germany and France, 33,000 sm of factories and 150 employees, Pozzoli S.p.A. is one of the most important companies in the Italian cardboard processing industry
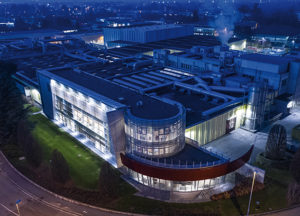
Traditionally recognized for the production of customized packaging for home entertainment market which still plays a dominant role today, the company has been distinguished throughout Europe for over 50 years for its innovative products with wow effect and for its complete service that incorporates values such as creativity, innovation and quality.
In the last decade, stimulated by a constantly evolving market, the company has experienced an extremely significant change both from the point of view of the reference business and in that of its organizational structure. The diversification of its products, resulting from a careful market analysis, has pushed the company to enter sectors such as high-end luxury perfumery, wine & spirits sector and, for some years, food sector.
Over the years, his attention to environmental sustainability has led the company to adopt an organization and a system of increasingly important and articulated certifications including: ISO 9001: 2015, ISO14001, ISO 45001: 2018 and ISO 22000 for certification in the food sector. The process, which is constantly updated, also includes those aimed at the French market: Ecovadis, Smeta and FSC/PEFC for the use of paper coming only from certified forests.
The company, already strongly customer oriented, in the face of the stimuli coming from an extremely prestigious clientele with high demands on its suppliers, is very attentive to the organized and computerized management of its business and makes use of partnerships that can support the company in the pursuit of this goal.
This is the push that brought Pozzoli S.p.A. to adopt Packway by B + B International 20 years ago.
Face to face with Emilio Cattaneo, chief HR & operations officer, and Mauro Drusian, supply chain manager
In recent years, the company made significant investments in terms of warehouse logistics. What goals drove these investments?
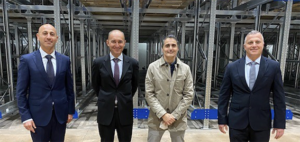
Dr. Cattaneo – “In addition to the box, the cluster, the casket and their aesthetic and functional presence, the multinationals of the brand owners demand a service that includes traceability of items, precise data, certifications, and basing on who is able to guarantee these quality standards, they choose their cardboard processing supplier. We have realized that we can serve a wide audience of international customers, focusing on everything that is recognized as value for the customer, which is commonly called service but which has reached very high levels. Through the construction of a highly automated warehouse with 2,720 pallet spaces, 34 tunnels for 20 pallets at 4 levels, which brought the storage capacity to 7,600 sm, elements such as time to market, on time delivery, traceability of raw materials, semi-finished and finished products have become the standard reference factors that increase the added value of the service that Pozzoli offers to its customers.
However, this investment has led at the same time to a great need to be able to manage all these processes at an IT level and to monitor in real time all the materials, semi-finished and finished products in every movement both inside and outside the company”.
How has Packway Logistica contributed?
Dr. Cattaneo – “The need was to have a unique and complete management software, capable of managing all business processes and with the inclusion of the Packway Logistica module we were able to achieve an exceptional result, always allowing us to identify the position of the material, never losing a pallet and delivering on time. Now we can easily respond to customer requests that require fragmented deliveries over long times and mix various orders based on delivery needs, as well as manage the finished products that customers themselves deliver to us for packaging: an extremely complex reporting system that thanks to this module we can make automatically. This inevitably translates into an improvement in the relationship with customers, in a loyalty process that tip the balance in the negotiation phase, managing to satisfy even those who pursue rigid and standardized protocols such as foreign customers”.
Dr. Drusian – “Packway Logistica module is mainly concerned with making every element of the warehouse traceable, not only for raw materials and finished products, but also for semi-finished products. In the management of the various business areas and in the development of production process, we create many semi-finished products that we can track, manage and store as well as identify when they pass from one machine to another. This precious possibility that this module gives us, allows us to be able to provide an even more detailed service to the customer, demonstrating to the auditors the traceability and control of the entire logistic production process. The possibility of being able to define the entire path of the movement unit (entry, passage between the various machines, manual work centers and exit) allows you to fulfill all the obligations that certification standards require.
We can calculate stock and turnover indices in extremely short times, understanding the information necessary in the right timing so that the financial means invested in goods are valued: this is an information of extreme value for us”.
What were the reasons that led you to introduce Packway by B + B International 20 years ago?
Dr. Cattaneo – The reasons that led us to introduce Packway are completeness and specialization. Completeness in being able to manage all our products, sometimes even very complex ones composed of various raw materials and different production processes, thanks to Packway’s graphic data sheet and completeness also in being able to truly manage all business processes with a single software, from CRM to shipments, passing through production, data collection from our 42 on-board terminals, up to integrated logistics. Specialization as Packway is developed for companies that produce packaging, this is an essential aspect of the software but also of the people, of the B + B consultants who speak the cardboard processing language, who support us in the implementation and training phases.
One of the corporate values is based on the high-level service offered to customers for high quality products. Ensuring a similar standard is equivalent to having to manage every activity of the company in a timely manner, translating it into controllable data. Making use of partners who support our operating mode both from an organizational/commercial and IT point of view with integrated systems, is what allows our business and our organization to be efficient, minimizing waste. This was the motivation that led us to forge an ever closer partnership with an interlocutor like B + B International back in 2001.
I would say that B+B itself grew up with us 20 years ago. We started by developing the customer service department, improving communications between sales and technical office and gradually we replaced all those software that managed certain areas in a sectorial manner, with an organic approach that would occupy and cover all sectors of the company.
Pozzoli has grown a lot over the years at an organizational level and has had to accompany this growth with an integrated IT system. We understood how indispensable it was in the company’s efficiency process to integrate IT systems safely and reliably to obtain reliable, available and easily usable information for our business intelligence”.
Dr. Drusian – “Before the inclusion of Packway, we had several not-integrated software to manage the various business areas, budgeting, production, accounting, etc. However, we realized, given the organizational and production complexity that distinguishes us, how necessary it was to have a complete system that could allow the whole company to communicate without losing even a single piece of data.
This need prompted us in the first instance to adopt a horizontal software of international standing from a well-known multinational software house, trying to customize it for our needs, but it was a very short-term project, because it did not conform to our needs. The difficulty we encountered in that experience was to find a partner who knew deeply the complexities of a cardboard processing company and who could serve us with specific software that was able to assist our structure, fitted to the cardboard processing needs, but declined on different visions that each business sector imposed. We needed a rigid but at the same time flexible software, which could be modeled on our operating methods.
When, after a careful and in-depth analysis, we realized that Packway’s technical data sheet allowed us to really manage all our product variables and complexities, we chose to undertake this path with B + B International, and still today we can say that we are satisfied with development continuity, software update and in general the service offered”.
What departments and functional areas are currently managed with Packway?
Cattaneo – “Packway is able to give us the answers we need and that are useful for the relationship with our customers. It supports the price definition activities and the organized and systematic budgeting policy by facilitating communication with the commercial area, allowing all this information to arrive in production with the launch of the order. This allows us to create a continuous and uninterrupted flow of information throughout the value building chain for our customer. We currently manage sales and technical offices with Packway CRM thanks to the digitization of all the necessary information and the planning of their activities. This allows us to have an immediate picture of the workload of our technicians, to make them participate and aware of the activities to be carried out for a certain date and then to define times and priorities.
In a complex business like ours, the real challenge we face is that every product we make in different sectors follows different production and supply chain logics. What is important to us and what we expect from our IT partner is that there is the same level of knowledge and data management for every product we make and for every job we launch.
In Pozzoli we produce a very large number of estimates, their processing must take place in a highly structured and equally fast way. The graphic data sheet is Packway’s engine because it simplifies the visualization of complex flows as the ones of our products are.
Estimate, order, commission, production and logistics are all children of the technical sheet. The completeness and strength of Packway is inherent in its ability to manage items with multiple raw materials and with transformation cycles that are also very different from each other, including the use of internal, external and semi-finished processes that must merge into a single product.
We have equipped the production with on-board terminals that instantly return the progress of the order with respect to the standards identified in the budgeting phase. On the one hand, this gives us a feel for how production is taking place and on the other, how the whole company is doing. It is precisely on the basis of this information that we are able to develop increasingly efficient and timely pricing policies, making our production processes more efficient.
In this way, the computer systems accompany us throughout the production process: today we have a systematic and instant indication of the production trends of each machine, important for the final accounting process, and for the collection of data in the production area as well as of the real performance of the company.
Quickly finalizing each order is essential for us to understand if the decisions we make every day are supported by solid foundations, this is what the Packway IT tool allows us and is the basis of our management control”.